AutoPasser
Generate Product Development, Northeastern University
Relevant Skills: electronics mounting, torque calculations, gearing
Objective
AutoPasser is an automatic hockey puck launching machine that enables players to practice without another individual present. As a second-phase project, our client tasked the team with reducing the footprint and weight of the original design. We were also required to increase puck firing speed and add a system to vary launch angle.
Variables / Constraints
My team had to work within a designated budget of $2000, and had a timeframe of approximately 3 months. The device had to fire pucks at no less than 20 mph, and needed to have at least 90 degrees of horizontal launch angle.
Role
As a Hardware Engineer, I was in charge of designing and incorporating the new system to vary launch angle. I also developed a motor driver mounting bracket and a display/user interface containment module.
Design Process
[1] I began by brainstorming different rotating mechanisms for varying launch angle. Since the turntable would have to support the firing, loading, and launching mechanisms, it needed to be robust and resistant to slippage. This led me to a large, custom gear with a stepper motor driven pinion over an actuator linkage or timing belt.
​

Actuator linkage test assembly

Timing belt pulley test assembly
[2] To proceed with the gear system, I needed to perform the necessary torque calculations to properly select a motor. For different angular accelerations, I determined the motor specs for both an aluminum and Delrin large gear. Due to weight constraints and the lower cost of machining, I decided to use Delrin. I communicated with the firing, loading, and launching teams to add in necessary mounting features on the Delrin gear. After review by the electrical team, the stepper motor was ordered as well. At the same time, I assisted in testing the flywheel launching system, which achieved speeds upwards of 53 mph.
​

Delrin gear model with partial teeth and mounting features

Gear with systems mounted on top, pinion mated
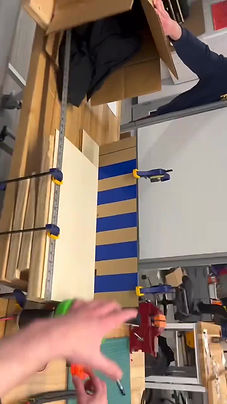
Testing of the flywheel launching system
[3] I selected a thin turntable to provide frictionless rotation for the gear while keeping the launching system close to the ground. With the stepper motor mounted, we tested the turntable mechanism, reliably achieving upwards of 120 degrees of rotation.
​
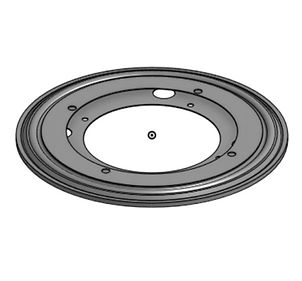
Turntable for mounting the large gear
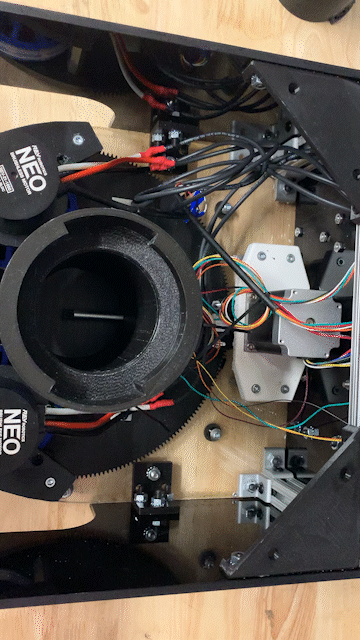
Motor system testing
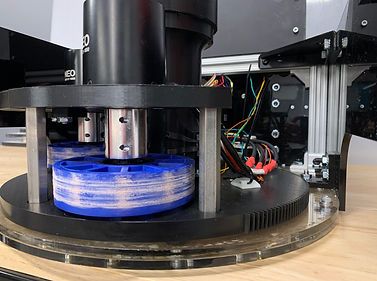
Turntable gear mounted on base of system
[4] I designed a mounting bracket to house all of the controllers and make cable management easier for the electrical engineers. Also, I built a screen and button mount to house the user inputs and PCB.
​

Screen and button mounting module, PCB housed inside

Motor driver and fuse containment bracket
Solution
The final assembly successfully decreased the size and weight of the first generation system and featured a working user interface and an adjustable turntable. My turntable system successfully provided over 120 degrees of launch angle without adding significant weight or cost to the system.
​
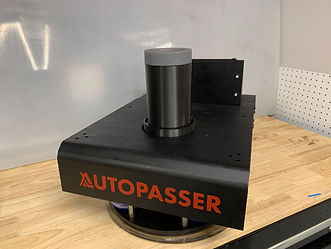
Final system, front view
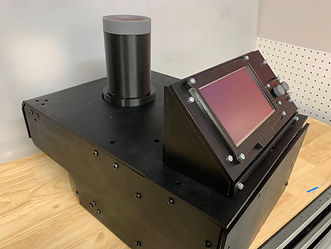
Final system, back view highlighting screen mount
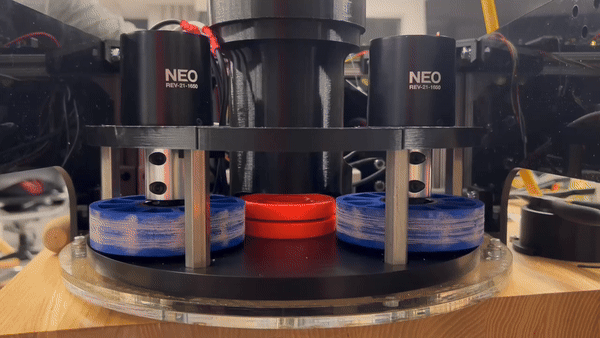
Rotating turret system on final product