Folding Universal Hybrid Skis
Capstone I and II, Northeastern University
Relevant Skills: material research, structural testing, advanced CAD
Objective
Design & prototype lightweight, foldable cross-country skis with universal binding compatibility.
Variables / Constraints
Since our client was the U.S. Army, the skis needed to support upwards of 400 pounds (equivalent to a fully kitted soldier). The skis had to withstand temperatures of -60°F since they were to be used in interior Alaska. The whole system had to be lightweight, and the binding solution needed to be compatible with a variety of low-temperature combat boots.
Design Process
[1] I began this project by performing extensive research on existing folding ski and universal binding solutions. As our client indicated, we noticed a gap in the ski market for a low-temperature ski that is capable of shrinking its footprint. Our contact within the Army highlighted the need for the skis and bindings to be easily actuated by a soldier wearing thick gloves, which guided our initial ideation. Early on, I determined that the hinge mechanism should be constructed from T5 titanium, while any plastic for the binding system should be Dupont Nylon.
​

Hinge sketch 1
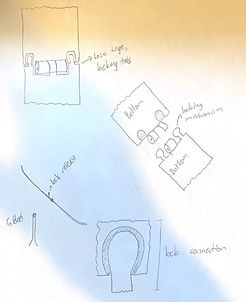
Hinge sketch 3
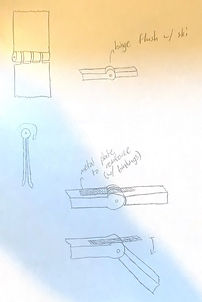
Hinge sketch 2

Hinge sketch 4
[2] After using a Pugh Matrix to determine the best design, I produce CAD for a simple, 2-stage hinging mechanism. This design involved 3 machined parts, two of which bolted directly to a pocket beneath the ski. The center hinge was attached by clevis/cotter pins. I set the material to 6061 aluminum since this is what the machine shop would construct our prototypes out of. By performing a static loading simulation with a load of 450 pounds, I achieved a safety factor of 0.7 for aluminum and around 8.0 for titanium.
​

Reduced footprint of folded ski

Close up view of 2-stage folding mechanism

Top view of stress distribution, static loading
[3] Since the simulation validated my design, I had it machined from 6061 aluminum. For the skis, we chose Nylon 101, which is the common homogenous material for modeling composite skis. As predicted by simulation, my design experienced slight plastic deformation at around 75% of the maximum 450 pound load. However, my design was still valid for titanium. This information, along with my groupmates' ski designs, helped to develop the final ski prototype.
​

Ski prototype, bottom, unfolded
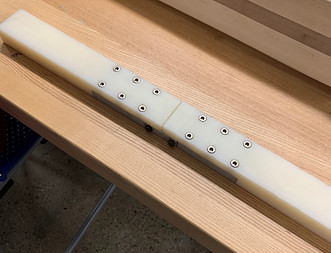
Ski prototype, top, unfolded
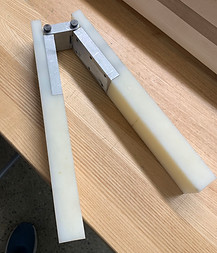
Ski prototype, side, folded

Instron static, fully reversed loading on prototype
[4] While developing the final hinge mechanism, I began work on the binding adapter. My goal was to create a low-profile, portable attachment to allow soldiers to seamless mount their combat boots to Telemark ATC bindings. After several iterations, I created an ergonomic binding adapter plate that reliably mated to the Telemark bindings and securely held the boot in place.
​

Binding adapter, 2nd iteration
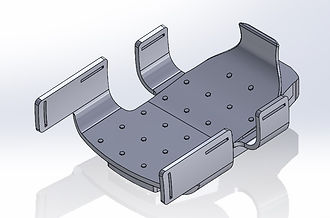
Binding adapter, 5th and final iteration
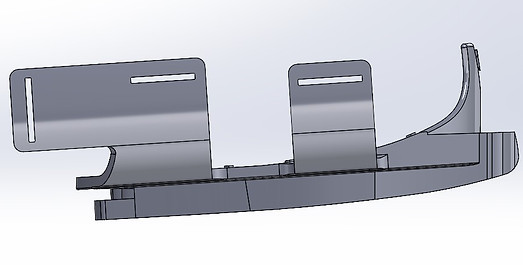
Binding adapter, 5th iteration, side profile
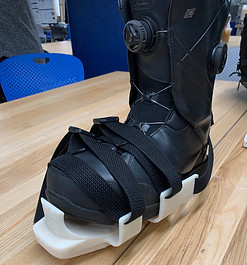
Boot secured in binding adapter
Solution
By combining the final hinge mechanism with the binding solution, my group and I successfully fulfilled the client's product criteria. Although prototypes were not made from the selected low-temperature materials, our simulations supported our design's validity at low temperature.
​

Binding adapter mounted on top of ski

Final hinge mechanism, unfolded view

Completed ski with Telemark ATC bindings

Final hinge mechanism, folded view