Fufu Pot
Generate Product Development, Northeastern University
Relevant Skills: project management, team leadership, sheet metal fabrication, metal machining, material selection
Objective
Fufu Pot is an appliance that automates the laborious process of making fufu, a staple in traditional West African cuisines. My team and I were tasked with creating a device to heat and mix fufu powder with the press of a button.
Role
Variables / Constraints
My team had to work within a designated budget of $1500, and had a timeframe of approximately 3 months. The device had to incorporate heating a high-torque mixing, all while fitting within the weight and footprint of other mixing appliances on the market.
As Lead Mechanical Engineer, I assigned my mechanical team of 4 to different subsystems of the project based on skills, goals, and interest. Throughout the semester, I mentored my teammates on topics such as material selection, 3D printing, gearing, tolerancing, and best CAD practices. I also consulted with the electrical lead to synthesize each subsystem.
Design Process
[1] Before the team began working, I met with the project lead and lead electrical engineer to develop a timeline. Through client communications, we identified key deliverables and developed a Gantt chart to guide our progress. I developed a detailed bill of materials and budget tracking document, and set up our shared Onshape CAD folder.
​
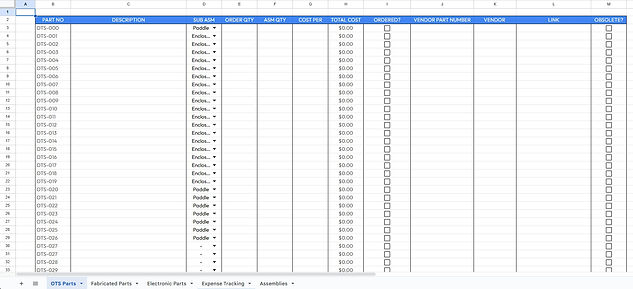
Excerpt from BOM and expense document
[2] After extensive test cooking sessions, we opted to use the modified planetary gear system of a stand mixer to create a motion capable of mixing the fufu flour. From our experimentation, I was able to select a brushless DC motor that provided sufficient torque for the mixing system. Another engineer and I researched gear reduction methods to couple the motor to the planetary system, ultimately deciding to use a 30:1 worm and worm gear. At the same time, I supported the frame design, which was constructed primarily from 80/20.
​
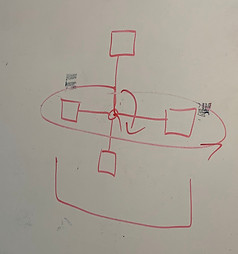
Rough sketch; overhead "pinwheel" mixing

80/20 frame for system

Rough sketch; planetary system

Rough sketch; Dual gear, quad paddle mixing system

Planetary mixing system from a stand mixer
[3] With the gears selected, I worked with the other engineers to secure the drivetrain in the top compartment of the system. On the worm and worm gear, I machined tapped holes for set screws, while I turned down the diameter of the planetary shaft using a lathe. I designed a horizontal shaft stabilizer and worked on a sheet metal motor bracket to prevent misalignment over time due to vibration. Due to machining capabilities, I designed non-structural panels to be laser cut from acrylic, while panels that bore a load or were subject to steam / heat were chosen as aluminum. Since inductive heating was used in the base of the machine, non-magnetic paneling was necessary to prevent the system from heating up.
​

Gearbox with 3D printed shaft stabilizers and metal motor bracket
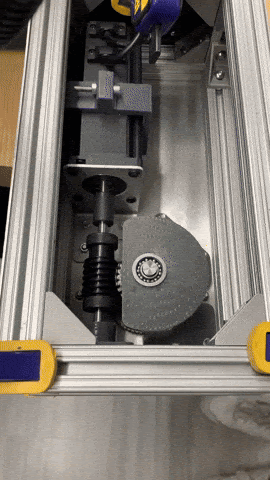
Motor system testing

Sheet metal motor bracket

CAD of drivetrain assembly

Horizontal shaft stabilizer
[4] Once the drivetrain was successfully tested, wires were routed from the inductor and motor to their respective controllers and the power supply. After organizing the cables, I installed the acrylic and sheet metal panels to close the assembly. Gasketing was placed between the frame and the panels to prevent steam from entering the system. I custom-ordered a plate of ceramic glass to serve as an induction stovetop.
​

Motor compartment with motor driver, cables routed and managed
Solution
By the provided deadline, the system was fully enclosed and provided reliable motor operation at the push of a button. The system was approximately the size and weight of a stand mixer as well.

Final product at the Generate Product Showcase
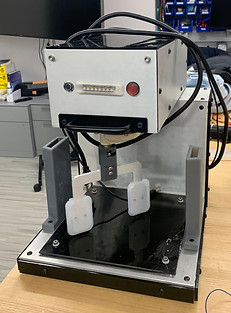
Final product

Operation of final product at Product Showcase