Electrodes and Electrode Clamp
Emphysys Inc.
Relevant Skills: precision machining (i.e reamers), biocompatible material selection, MJF printing, rapid prototyping
Objective
Design and create an electrode that can fit inside a well plate and is capable of generating an electric field of given strength on the bottom of said well plate.
Variables / Constraints
The electrodes needed to be biocompatible and thus impervious to an ethanol wash. Different versions had to be created with electrode spacing of 1mm, 2mm, 5mm, 8mm, and 10mm, with a margin of error no greater than ±0.15mm. The electrodes had to sit flush on the bottom of the well plate to deliver an electric field to a thin film of living cells.
Design Process
[1] I was given the previous iteration of electrode to begin with, which used hollow surgical tubing as the electrodes. Unless the electrode was inserted into the well plate very precisely, one or both electrodes would not contact the bottom, causing test failure. To ensure that the electrodes contacted the bottom of the well plate, I decided to use spring-loaded cup point test probes as electrodes. Since these would be under constant compression, the springs would press the electrode tips against the well plate.
​

Spring-loaded test probe

Well plate used for testing - also called a cell culture plate
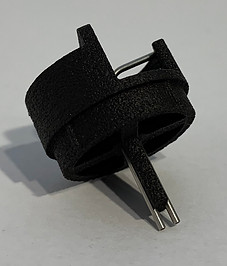
Previous electrode iteration
[2] With the electrodes selected, I began to develop the housing to secure them. I added more material on the top for easier handling and expanded the crush ribs on the bottom to improve alignment and increase friction against the well plate.
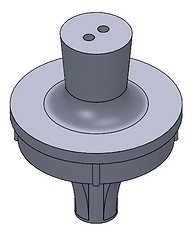

First prototype: Knob for easy removal from well plate
Second prototype: Lengthened crush ribs, barrier to prevent arcing between electrodes
[3] I began to rework the electrode to include a flat surface at the top to accommodate an external clamping force. After testing fitment with an SLA print, I made slight adjustments and had the electrodes made from polypropylene due to its biocompatibility. Using precision reamers, I properly sized the holes to accept the electrodes. Preliminary tests with the PP electrodes on live cell cultures were successful.
​

Third prototype: flat clamping surface added on top

Resin print of third prototype

Fourth prototype: DFM, larger rim added for more well plate contact

PP electrodes with soldered-on leads
[4] In unison with the electrode development, I created and constructed a clamping platform to hold the electrodes in place on the well plates. To allow every well in the plate to be accessible, I opted for an overhead gantry design mounted on an ABS plate. The first design utilized a toggle clamp on a large, 3D printed gantry. Due to print bed sizes and biocompatibility issues with resins, however, I changed the gantry to be made of aluminum extrusions and an aluminum plate.
​
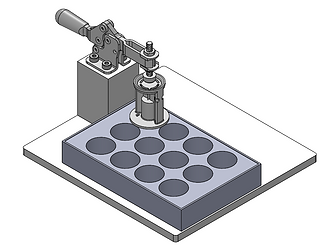
Conceptual design, not used since clamp cannot reach inner cells
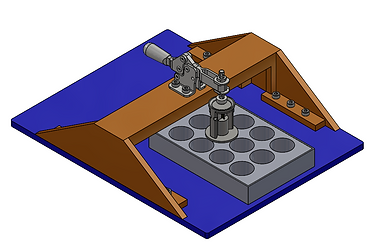
First prototype: 3D printed gantry

Final design: Gantry constructed from aluminum and ABS
Solution
I reamed a final batch of electrodes made from MJF Nylon-12, which yielded even more accurate electrode spacing. During the ethanol wash, previous dyed MJF prototypes leached color, so I printed undyed models, under sizing the electrode holes to accommodate less material. The final electrodes succeeded in providing constant cell layer contact at precise spacings, all while being biocompatible.

Final electrode design with 10mm, 8mm, and 5mm spacing (left to right)
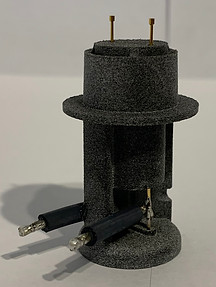
Close-up of final electrode with soldered-on leads

Clamping platform test fixture with electrode and well plate in place